Hearing Testing Without Production Downtime: Yes, It’s a Thing!
Deanna Lennox • August 9, 2022
Stop Losing Production Time!
Would you let someone from outside of your organization take one of your employees away from their workstation during production time, possibly with no time limit?
The request sounds so unthinkable that most employers would not even respond without more information, yet it happens to an estimated 80% of employers.
When hearing tests are done at an employer’s site for OSHA compliance, an uncharacteristically passive attitude is adopted by management and the test provider is allowed to have an employee for 20-30 minutes, sometimes even more. The test provider may suggest a time estimate for the session but is not accountable to have the employee back by any specific time. Paying ½ an employee’s hourly wages multiplied by 50, 250, or more employees can obviously run into thousands of dollars, but there are even more important considerations.
If one person is gone for 5-10 minutes, the absence can be absorbed, but groups of 4-8 people gone for 20-30 minutes significantly interrupts productivity. The financial loss to the owners or shareholders is far more than just the cost of hourly wages lost, it includes the plant’s output being diminished while the overhead costs that go with it stay as high as ever.
Daily production-
A management goal is to achieve a forecasted amount of output in a day. A facility’s systems, methods, software, and workflow all synergize to achieve this forecast. The Company depends on this as the planned daily net profit to owners often equals less than 5% of a day’s production. At financialrhythm.com’s (Campbell, 2020) average net profitability by industry post, Steel and paper/forest products are at 4% and 2% net profit respectively. Using an average of 3%, companies in these industries with $100,000 in daily output would plan for $3000/day in net profit. That is when production is at 100% of the planned rate- things going perfectly. Hold this $3000 in mind while considering the following 2 cases in the Northwestern USA:
1) Auto Battery manufacturer:
A manufacturer of automotive batteries in the Northwest produces batteries on 3 production lines. Manta.com
(2019 Manta Media Inc., all rights reserved, 2019) indicates annual revenue of $50-100 million, so it can be said that daily production would be $300,000 if the annual revenue was $75 million.
Their hearing tests were being done 4 people at a time, which impacted production to the point that one of the 3 battery lines had to be shut down. Simple math can be used to see what would happen to $300,000 daily revenue if one of three lines got shut down, suffice it to say they were looking for alternatives. In 2019 they changed to doing hearing tests one at a time, and the plant manager’s report was “…not a ripple in production”. Restoring $100,000 to output daily was very attractive
2) Window manufacturer:
A window manufacturer in the NW has committed to LEAN manufacturing principles. They have closely measured their processes, and monitor output knowing the importance of hitting targets. They did on-site hearing testing 4-at-a-time and learned from their monitoring system that production was clearly down by 15%. That 15% cost far more than what the hearing test provider charged.
3) Exotic Metal Casting company:
During annual hearing tests for 350 employees, top management at a castings company looked out of their upper window and noticed a bad sight in the parking lot. 4 employees were in a truck, and 8 others were gathered near it- some recently finished and some waiting their turn. Instinctively recognizing the cost to the organization of this grouping, direction was handed down that changes must be made. They began testing one at a time and the disruption stopped.
LEAN manufacturers may be able to see the costs and benefits more clearly than others, but it affects all employers. The mistake at the core is that hearing test providers have built an expectation that they can show up and take control of the workforce with no one holding them accountable, holding employees - and production
- hostage to their own production schedule. Somehow it has become usual and customary to make their schedule the priority. Testing one at a time puts control back in the employer’s hand.
That is the method used by many employers with over 500 people, but now it can be insourced along with all the profitability.
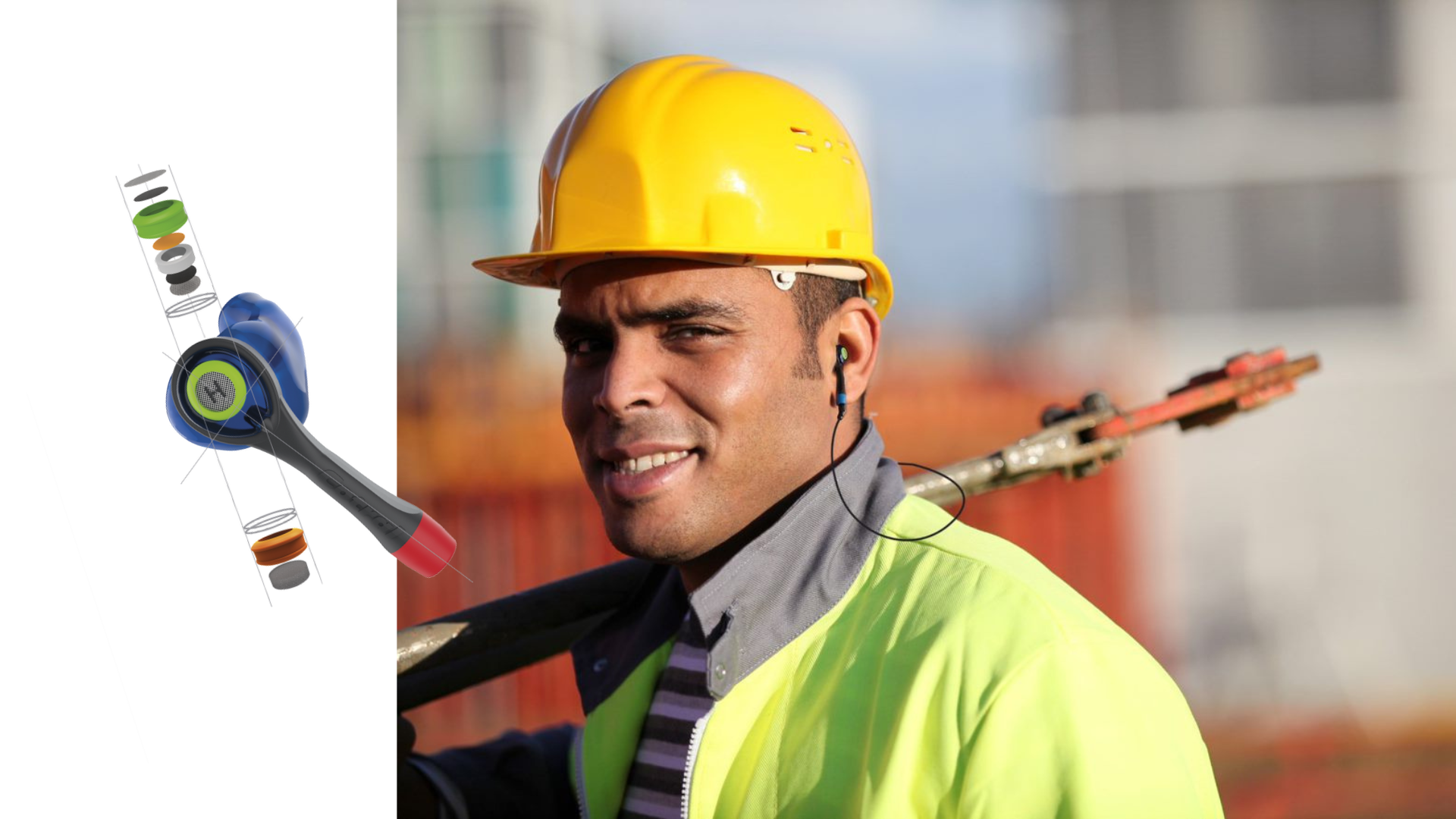
There are thousands of industrial hearing protection options out there - which type of noise blocking is right for your employees? Our filtered industrial hearing protection combines the best of electronic hearing protection & solid hearing protection devices, ensuring your employees can communicate safely without the hassle of electronics.